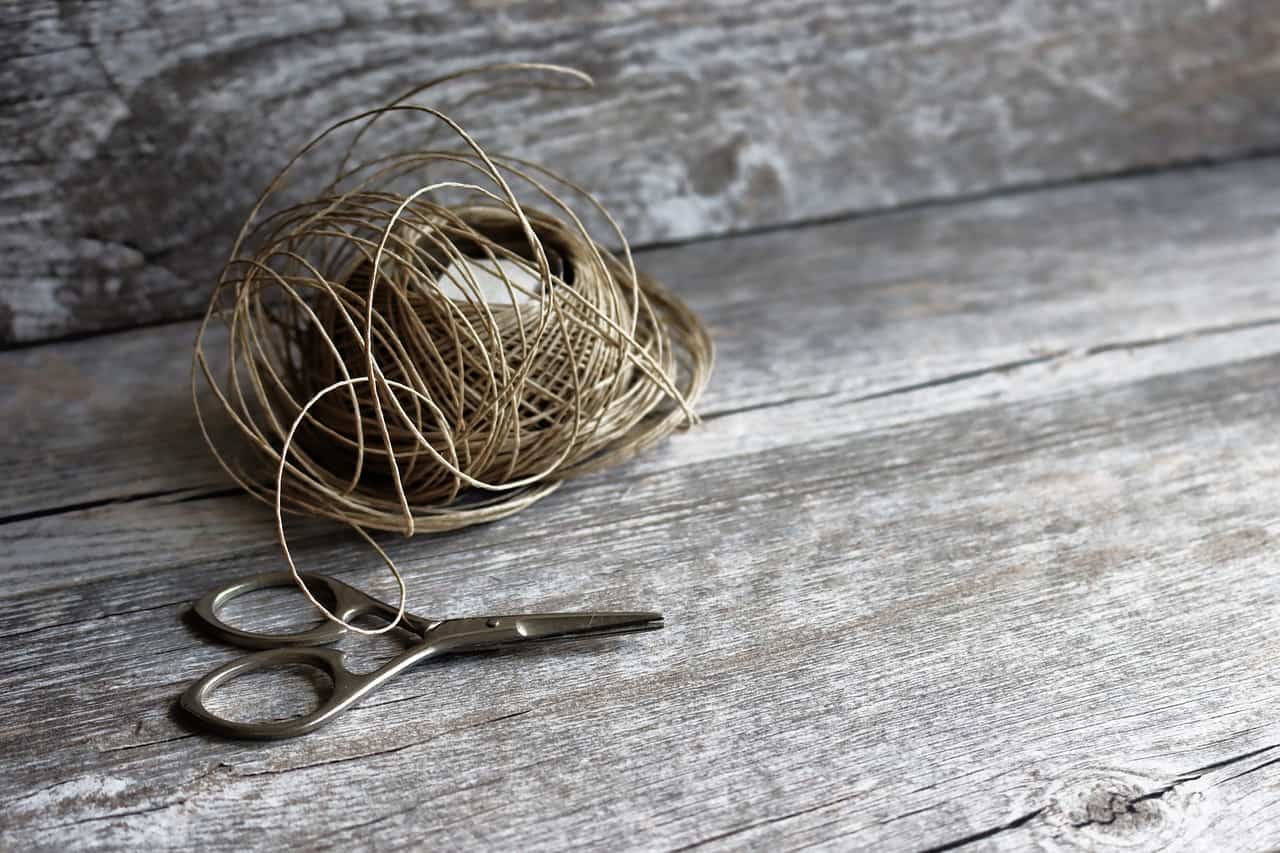
Industrial Uses of Hemp Fibers
Definition of Hemp
Hemp, scientifically known as cannabis sativa, is a versatile plant that has been cultivated for thousands of years for various purposes.
Industrial hemp refers to specific varieties of cannabis sativa that are grown for their fibers, seeds, and stalks, rather than their psychoactive properties. Hemp fibers are one of the key components of the plant that are widely used in different industrial applications. These fibers, extracted from the outer layer of the hemp stalks, possess unique properties that make them suitable for a wide variety of uses.
From building materials to animal bedding, the potential of hemp fibers is vast, and they are increasingly recognized as a valuable renewable resource. The production of industrial hemp is gaining momentum worldwide, with countries like the United States becoming major players in this agricultural commodity.
The physical and mechanical properties of hemp fibers, along with their eco-friendly and sustainable nature, have sparked interest in their application in composite materials, natural fiber composites, and other industrial sectors. The potential of hemp as a multifunctional material holds promising opportunities for a greener and more sustainable future.
History of Hemp
Hemp has a rich history as an industrial crop, dating back to the mid-18th century. During this time, hemp production thrived in Europe and the Americas, with the plant being widely cultivated for its versatile uses. However, the rise of synthetic fibers and the prohibition of cannabis sativa, the hemp plant, in the 20th century led to a decline in its production.
In the United States, the Marihuana Tax Act of 1937 and the subsequent Narcotics Control Act of 1956 effectively banned hemp cultivation, treating it the same as marijuana. However, during World War II, the federal government temporarily lifted the prohibition due to a need for fiber for the war effort. This led to a brief revival of hemp production, with farmers encouraged to grow the crop. However, after the war ended, hemp returned to being illegal.
In Europe, a similar decline in hemp production occurred. The invention and widespread use of synthetic fibers in the mid-20th century posed a serious challenge to the natural fiber industry. As a result, hemp cultivation became less economically viable, and many farmers shifted to other crops.
However, in recent years, there has been a renewed interest in industrial hemp. Recognizing the potential of hemp and the demand for sustainable and eco-friendly materials, many countries have reconsidered their prohibition policies and have started to reintroduce hemp cultivation. With its wide variety of applications, including in building materials, animal bedding, and composite materials, hemp is once again being recognized as a valuable agricultural commodity.
The history of hemp production has been marked by periods of prosperity and decline, influenced by legal restrictions and the emergence of alternative materials. As governments and industries continue to explore the potential of hemp, it is expected to play an increasingly significant role in the future of sustainable and environmentally-friendly industrial production.
Overview of Industrial Uses of Hemp Fibers
Industrial uses of hemp fibers span across various industries, including food, fiber, fuel, and more. Hemp fibers have gained popularity due to their versatility and sustainability.
In the food industry, hemp fibers are used to produce a wide range of products. Hemp seeds are a nutritious superfood, containing high levels of omega-3 fatty acids, protein, and essential vitamins and minerals. Additionally, hemp fibers are used in the production of hemp oil, which has a variety of culinary and dietary uses.
The fiber industry utilizes hemp fibers for manufacturing textiles, papers, and composites. Hemp fibers are strong and durable, making them ideal for the production of clothing, ropes, and other textile products. Hemp paper is also highly sustainable, as it requires less water and fewer chemicals compared to traditional paper made from trees.
Hemp fibers are also used in the fuel industry. Hemp can be converted into biofuels such as biodiesel and ethanol, offering a renewable and environmentally friendly alternative to fossil fuels.
Furthermore, hemp fibers have numerous industrial applications. In construction, hemp fibers can be used as insulation materials, providing an eco-friendly and energy-efficient solution. In the personal care industry, hemp fibers are used in the production of cosmetics, skincare products, and even biodegradable packaging.
The industrial uses of hemp fibers are vast and diverse. From food to fiber to fuel, hemp fibers offer a sustainable and environmentally friendly alternative in various industries. Their versatility and eco-friendly properties make them a valuable resource in the pursuit of a greener future.
Properties of Hemp Fiber
Hemp fibers possess a multitude of unique properties that make them highly valuable in various industrial applications. One of the most notable properties of hemp fiber is its strength and durability. Hemp fibers are known to be stronger and more resilient than many other natural fibers, such as cotton or flax. This makes them ideal for the production of textiles, ropes, and other products that require high tensile strength.
Additionally, hemp fibers are highly absorbent, allowing them to retain moisture and regulate temperature. This property makes them suitable for use in items like bedding and insulation materials. Hemp fibers are also naturally antimicrobial, making them resistant to mildew and mold growth. This quality is beneficial in the production of textiles and other products that may come into contact with moisture.
Another important property of hemp fiber is its sustainability. Hemp is a fast-growing crop that requires minimal water and chemical inputs for cultivation. The plant is also highly versatile, as it can be grown in a wide range of climates and soil conditions. This makes hemp a highly sustainable and eco-friendly option compared to many synthetic fibers.
Tthe properties of hemp fiber, including its strength, absorbency, antimicrobial qualities, and sustainability, make it an excellent choice for a variety of industrial uses. From textiles to insulation materials, hemp fiber offers numerous benefits that contribute to a more sustainable and environmentally friendly approach in various industries.
Physical Properties
Hemp fibers possess several physical properties that contribute to their wide range of industrial uses. One of the most notable properties is their high tensile strength and durability. Comparatively stronger and more resilient than natural fibers like cotton or flax, hemp fibers are ideal for manufacturing textiles, ropes, and other products that require robust strength.
In addition to strength, hemp fibers exhibit excellent moisture absorption capabilities. They can retain moisture and regulate temperature effectively, making them suitable for use in bedding materials and insulation products. Moreover, hemp fibers are naturally antimicrobial, making them resistant to mold and mildew growth. This characteristic is advantageous in the production of textiles and other items that may come into contact with moisture.
Another significant physical property of hemp fibers is their sustainability. Hemp plants are highly versatile and can be cultivated in a wide range of climates and soil conditions. Moreover, they require minimal water and chemical inputs for growth, making hemp a highly sustainable and eco-friendly option compared to synthetic fibers.
The physical properties of hemp fibers, including strength, moisture absorption, and sustainability, make them an excellent choice for various industrial applications such as textiles, insulation, and more.
Chemical Properties
Chemical Properties of Hemp Fibers
Hemp fibers possess unique chemical properties that contribute to their strength, durability, and resistance to pests, mold, and mildew. The composition of hemp fibers includes various chemical components that lend these fibers their exceptional characteristics.
Cellulose is a major chemical component of hemp fibers, constituting around 50-70% of their composition. This polysaccharide contributes to the high tensile strength and durability of hemp fibers, making them suitable for numerous industrial applications. Additionally, cellulose acts as a natural insulator, providing thermal properties to products made with hemp fibers.
Hemp fibers also contain lignin, a complex organic polymer that offers structural support and rigidity. Lignin contributes to the overall strength and stiffness of hemp fibers, making them resistant to tearing and breaking.
Furthermore, the chemical composition of hemp fibers includes cannabinoids, specifically CBD (cannabidiol), and terpenes. These compounds are responsible for the natural resistance of hemp fibers to pests, mold, and mildew, making them ideal for products that require antimicrobial properties.
In the production of hemp fibers, various chemical treatments and processes are involved. These can include enzymatic hydrolysis to separate the fibers from the plant’s outer layer, as well as dew-retting or hackling to extract the fibers from the stem. These treatments further enhance the quality and performance of hemp fibers.
The chemical properties of hemp fibers, such as their cellulose content, lignin composition, and presence of cannabinoids, contribute to their strength, durability, and resistance to pests, mold, and mildew. The utilization of chemical treatments in the production process further enhances the quality of hemp fibers, making them a highly desirable and sustainable raw material for various industrial applications.
Textural Properties
The textural properties of hemp fibers contribute to their overall usability and suitability for various industrial applications. These properties include both tactile characteristics and physical structure.
In terms of texture, hemp fibers can range from coarse to smooth, depending on their processing and intended use. Coarser fibers are often used in applications such as animal bedding or hempcrete, where their rough texture provides insulation and durability. On the other hand, smoother hemp fibers are commonly used in textiles and fabrics, as their softer texture makes them comfortable against the skin.
The length and width of hemp fibers can also influence their textural properties. Longer fibers are typically preferred for applications that require strength and flexibility, such as composite materials or rope production. On the other hand, shorter fibers may be used for applications where a finer texture is desired, such as paper production.
In terms of appearance, hemp fibers have a natural, earthy look that adds character to products made with them. They can vary in color, ranging from creamy white to light brown, depending on the hemp variety and processing methods.
The textural properties of hemp fibers make them versatile for a wide range of industrial uses. Their coarseness, smoothness, length, width, and unique appearance contribute to their suitability in applications such as textiles, paper, composites, and construction materials.
Thermal Properties
Thermal properties of hemp fibers play a crucial role in their suitability for various industrial applications. Hemp fibers exhibit good heat resistance and stability, making them ideal for use in thermoplastic and thermoset composites.
When subjected to heat, hemp fibers have a relatively high thermal stability, allowing them to retain their structural integrity. This property ensures the fibers can withstand processing temperatures, such as during molding or curing processes.
In terms of matrix selection, hemp fibers can be combined with both thermoplastic and thermoset polymeric matrices. Thermoplastic matrices, such as polypropylene or polyethylene, can be melted, reshaped, and recycled multiple times without significant loss of properties. This provides flexibility and ease of processing for manufacturers.
On the other hand, thermoset matrices, such as epoxy or polyester resins, offer enhanced mechanical properties and better resistance to chemicals and solvents. Once cured, thermoset composites cannot be melted or reshaped, making them better suited for applications requiring higher strength and durability.
The choice between thermoplastic and thermoset matrices for hemp fiber composites depends on the specific requirements of the application. Thermoplastic matrices offer easier processing and recycling, while thermoset matrices provide superior mechanical properties and chemical resistance.
Hemp fibers have favorable thermal properties that make them compatible with both thermoplastic and thermoset matrices. The selection of the matrix depends on the desired application, balancing factors such as ease of processing, recycling capabilities, and mechanical performance.
Durability and Strength
Hemp fibers exhibit remarkable durability and strength, making them highly suitable for various industrial applications. These natural fibers possess excellent mechanical properties, including high tensile strength and resistance to wear and tear. When compared to synthetic fiber composites, hemp fibers offer several advantages in terms of mechanical strength, durability, flexibility, heat resistance, and corrosion resistance.
In industrial settings, hemp fibers are often used as a reinforcement material in composite structures, providing enhanced mechanical strength to the end product. The fibers can be combined with different matrix materials, such as thermoplastics or thermoset resins, to create strong and durable composites. Due to the robustness of hemp fibers, these composites demonstrate higher strength and stiffness, making them ideal for applications requiring structural integrity.
Hemp fibers also excel in flexibility, allowing for efficient molding and shaping processes in the manufacturing of various products. Their ability to withstand processing temperatures makes them suitable for applications involving heat exposure. Additionally, hemp fibers exhibit excellent resistance to corrosion and degradation, prolonging the lifespan of the end products and reducing maintenance costs.
One notable industrial use of hemp fibers is in building materials. Hempcrete, a composite material made from hemp fibers and a binder, is used for construction due to its outstanding insulation properties. The hemp fibers provide better insulation and noise absorption than traditional building materials, contributing to energy efficiency and acoustic comfort.
Hemp fibers offer exceptional durability and strength, surpassing synthetic fiber composites in various industrial applications. Their mechanical properties, flexibility, heat resistance, and corrosion resistance make them an excellent choice for industries seeking reliable and sustainable solutions. The use of hemp fibers in building materials, such as hempcrete, further reinforces their potential for enhancing insulation and noise absorption properties.
Agricultural Production of Hemp Fibers
Agricultural production of hemp fibers refers to the cultivation and harvesting of hemp plants for the specific purpose of extracting and utilizing their fibrous stalks.
Hemp is prized for its versatile and sustainable fiber properties. With a history spanning thousands of years, the cultivation of hemp fibers has been embraced by various industries for its wide range of applications. As an agricultural commodity, hemp offers numerous advantages, such as high yields, efficient land use, and low environmental impact.
From industrial uses in the production of textiles, paper, and building materials to applications in animal bedding and animal feed, the agricultural production of hemp fibers holds immense potential for meeting various commercial and industrial demands. As research continues to uncover the exceptional qualities of hemp fibers, agricultural producers are increasingly recognizing the value and economic viability of including hemp in their crop rotations.
The growth of the hemp industry holds promise for sustainable agriculture and the development of environmentally friendly products.
Cultivation Processes
Cultivating industrial hemp fibers involves several important processes. First and foremost, it is crucial to select the right agro-ecological conditions for hemp cultivation. Hemp thrives in regions with warm summers, moderate rainfall, and well-drained soil, although it is adaptable to various climates. Additionally, hemp can be grown as a monocrop or intercropped with other plants, allowing for diverse crop rotations.
The cultivation of hemp fibers involves different types of crops, depending on their intended use. Some hemp varieties are specifically cultivated for their long and strong fibers, while others are grown for their seeds, oil, or cannabinoids. Varieties with high fiber content are preferred for industrial purposes, such as the production of building materials, textiles, and composites.
Factors that influence the plant architecture of hemp varieties and clones include genetics, growing conditions, and cultivation techniques. Plant height, stem diameter, branching pattern, and internode length can all vary depending on these factors.
Hemp cultivation offers high yields and several environmental benefits. The plant’s rapid growth and dense foliage suppress weeds, reducing the need for herbicides. Moreover, hemp’s extensive root system helps prevent soil erosion and improves soil structure, contributing to overall soil quality. Additionally, hemp requires fewer pesticides and fertilizers compared to other crops, making it an environmentally friendly choice.
Cultivating hemp fibers involves selecting suitable agro-ecological conditions, choosing the right crop type, considering plant architecture factors, and reaping the benefits of high yield and environmental advantages.
Varieties Available for Cultivation
When it comes to hemp cultivation, there are different varieties available, each serving various purposes.
Fiber hemp is specifically grown for its long and strong fibers, making it suitable for industrial uses like building materials and textiles. This variety typically has taller stalks and fewer branches.
Oilseed hemp, as the name suggests, is cultivated for its seeds, which are rich in oil. These seeds can be used for cooking, making cosmetics, or producing biofuels. Oilseed hemp varieties tend to have a more bushy and compact growth pattern.
CBD hemp is grown for its high levels of cannabidiol, a non-psychoactive compound found in the cannabis plant. The flowers and leaves of CBD hemp are harvested for their medicinal properties and are commonly used in health and wellness products. CBD hemp plants often have a similar appearance to oilseed hemp with their bushy growth.
When planting different types of hemp crops, planting density requirements may vary. Fiber hemp, with its taller stature, may require a wider spacing between plants to allow for ample airflow and light penetration. Conversely, oilseed and CBD hemp plants can be grown closer together due to their compact growth.
There are various varieties of hemp available for cultivation, each with its own unique characteristics and growth patterns. Whether it’s fiber hemp, oilseed hemp, or CBD hemp, farmers have options based on their specific needs and desired end products.
Largest Producers in the World
Based on research, the largest producers of hemp fibers in the world are Canada, China, and the European Union. Canada is recognized as the largest producer and exporter of industrial hemp, with an estimated fiber production of over 70,000 tons in recent years. China follows closely, with its extensive hemp cultivation and advanced processing capabilities. The European Union is also a significant producer, with countries like France, Germany, and the Netherlands leading the way in hemp fiber production.
The average yield of hemp fibers per acre can vary depending on factors such as cultivation practices and varieties grown. On average, hemp fiber production ranges from 2 to 5 tons per acre, making it a highly productive and sustainable raw material.
Hemp fibers have numerous applications in the textile industry due to their exceptional properties. They are lightweight, breathable, and possess great tensile strength, making them ideal for producing fabrics, ropes, and twines. Additionally, hemp fibers are known for their durability and ability to withstand frequent washing and prolonged use. The textile industry can benefit from incorporating hemp fibers into various products like apparel, upholstery, and even industrial textiles.
Canada, China, and the European Union are the largest producers of hemp fibers in the world. With its high yield per acre and versatile applications in the textile industry, hemp fiber production holds great potential for meeting the increasing demand for sustainable and eco-friendly materials.
Industrial Uses of Hemp Fibers
Hemp fibers have a wide range of industrial applications, making them a versatile and sustainable choice for various industries. One of the notable uses of hemp fibers is in the production of paper. Hemp paper is renowned for its durability and longevity, making it ideal for books, stationary, and packaging materials. Compared to wood pulp paper, hemp paper requires fewer chemicals and energy during production.
In the textile industry, hemp fibers are highly valued for their strength and breathability. They can be used to create fabrics, ropes, twines, cables, carpets, sailcloth, and canvas. Hemp fibers are even stronger than jute and linen fibers, making them perfect for applications that require high tensile strength.
Hemp fibers are also utilized in the production of biodegradable plastics. These plastics have a lower environmental impact compared to traditional petroleum-based plastics and can be used in various industries, including packaging and automotive.
Furthermore, hemp fibers are a valuable ingredient in health food products. Hemp seeds, which are rich in protein, omega-3 fatty acids, and fiber, can be ground into flour, used as an ingredient in protein bars, and added to smoothies.
Overall, hemp fibers have a wide array of industrial uses, including paper production, textiles, biodegradable plastics, and health food products. Their strength, durability, and sustainability make them an environmentally friendly choice for various industries.
Total reviews
Persons recommended this product
Filter by
star Rating
attach_file Attachments
Anonymous
Shopper
check_circle Verified
Shop owner replied
Was this helpful
Facebook
X (Twitter)
LinkedIn
Reddit
Copied to Clipboard
Anonymous
Shopper
check_circle Verified
Shop owner replied
Was this helpful
Facebook
X (Twitter)
LinkedIn
Reddit
Copy Link
Thanks for your review!
Your feedback helps us improve our service.
There are no reviews yet.
Be the first to review “ ”
Only logged in customers who have purchased this product may leave a review